For the first time in the whole world, we make a facsimile edition of the Papyrus of Ani in authentic natural papyrus collected and brought directly from the Nile. Just like it was 3000 years ago.
Now, we want to answer some of the questions about this masterpiece:
How is our facsimile presented?
cARTEm presented the facsimile in a luxurious wooden coffret with gold scarab decoration on the lid. It is the ideal way to better preserve it. In addition, its design allows the structure itself to become a stand for an optimal contemplation.
“We had to create a completely flat box to prevent humidity from entering. We have even designed a box, similar to a sarcophagus. The objective is house the work and a stand so that the reader can turn the pages”, Daniel Díez, editorial director of cARTEm.
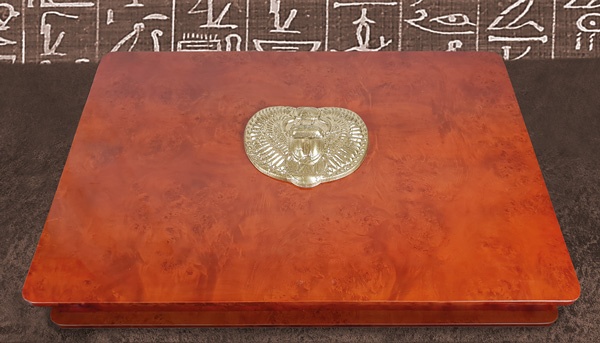
Which techniques have been used to make our facsimile?
This is not the first attempt to reproduce The Papyrus of Ani. But until now, technology wasn't be able to recreate the colors and textures of the original material.
“The process of dealing with the rips in each section could be time consuming. Each photograph has a resolution that ranges between 150 MP and 200 MP. This image quality was impossible to achieve 10 years ago. But the cameras we use for this project are gigantic, like scanners, up to 5 meters,. This allow us to obtain this resolution. Assemblying the scanner can take us a whole day”.
We used ultra-high-resolution cameras and a last generation laser cutting machine to deal with every single rip. Also to get such an extraordinary quality facsimile that it is impossible to distinguish it form the original.
A perfect copy
We have reproduced every single detail, including the traces of the damages caused by the passage of time and humidity stains. That makes this facsimile a true masterpiece.
The use of modern technology has allowed us to “define with precission the small flaws of the original. And, furthermore, the edges are a clear reflection of the parchment that preserved in the British Museum."
The technical part, undoubtedly, was one of the most complex matters. Not only the papyrus, we also analised the colors and the texture in detail, the images also reproduce the History. From the definition to the papyrus threads.
“After the first images we have reinforced the white. For example, since the Egyptians used a very strong white. Basically, they used natural pigments, white from lime. In nature there are two sources for blue: lapizlazuli, and cobalt, while red is obtained from clays and green from natural pigments.
For the texture and density of these types of pigments, the objective was to recreate that alive look, that’s why we searched son intensely for a technique that would allow us to reproduce this 3D look." said Daniel Díez.
How long did it take us to complete this facsimile edition?
So, to produce the 999 copies of this limited and notarized, first facsimile edition, we needed more than 3 years of specialized work.
“Original Papyrus of Ani made using amaterial where it is not possible to print on directly. It being a hard work finding a substitute for this purpose. But after a few years we discovered a possibility to do so. We brought papyrus from Egypt, we did tests and requested necessary permissions to the British Museum to reproduce the work”. Daniel Diez
Papyrus has traveled almost 4000 km to Spain
The papyri is imported, brought in different batches from Egypt. We have respected measurements and imperfections, with an absolute fidelity to the original.
The process began with the first tests on the authentic papyrus from Egypt. Followed by many trips to the British Museum (where the original is under strict security measures), to request reproduction permits and photograph the work, as well as endless tests to get a perfect result. We must add to all this, the enormous difficulty to reproduce the exact tones used to illustrate the original texts.
What was the most difficult part of reproducing this facsimile?
"The most difficult thing was the logistics to obtain, manage, import and deal with the natural Egyptian papyrus: more than 72,000 sheets," explains Díez.
Nearly a hundred people have worked on the complex processes to complete the edition, to photograph, reproduce, print, illustrate and assemble each copy by hand at a parsimonious pace which allowed us to produce four copies per week in its final phase. “Handling the papyrus, adjusting the colors or reproducing in gold one of the beetles in the book have been just some of the challenges,” explains Díez.
In addition, we recalibrated the printer papyrus by papyrus, because the Papyrus had a light color. But it darkened due to the passage of time or due to the fact of being rolled and the inaction of light, and this should be exactly reproduced in our facsimile.
Which materials were used to make our facsimile edition of the Papyrus of Ani?
One of the biggest curiosities was the type of material used to create our facsimile edition of the Papyrus of Ani.
That’s why we want to share with you these pictures where you can see how sheets of papyrus arrived from Egypt, cut to the exact measure we needed to make our facsimile edition of the Book of The Dead.
As something curious, we have to mention that cARTEm is nowadays the main importer of natural papyrus in Europe, according to our supplier in Cairo.
Papyrus only grows on the banks of the Nile River
For thousands of years papyrus was the main material where to write on. Therefore a key piece for the transmission of culture and knowledge. With the blockage of the Mediterranean by Islam, its use began to decline gradually until the 11th century, when it was no longer used for writing or illuminating texts.
Papyrus can only grows from strips of the stem of the plant that bears its name and grows on the banks of the Nile River. Once the strips of the plant stem are made, they are soaked to soften them and then pressed, alternating the direction of the fiber, to get a flat and compact support on which the beauty of the images can be reflected.
When we receive an order, we have to “rebur” or trim with very thin blades the excess of fiber of every sheet of papyrus in order to start printing with guarantees of reaching the highest quality and definition.
One of the most and durable supports ever known
Once the papyrus is made, it becomes one of the most solid and durable supports ever known. It is almost impossible to break it by exerting pressure or pulling on the ends.
This is because during the pressing process, the plant sap acts as a natural glue. Giving the structure an extraordinary consistency. We have made our facsimile edition on this natural, sustainable, ecological, resistant and durable material.
In conclusion, we didn’t choose the materials by chance, since we wanted our reproduction to be at the same level as the original, kept in the British Museum, and which is, undoubtfully, the most spectacular and important decorated papyrus that has survived to this day.
Do not hesitate to contact us to request more information about the process of making it and about the notarized and numbered print run, limited to 999 copies.